Исследование влияния волластонита Верхне Бадамского месторождения на свойства эластомерно
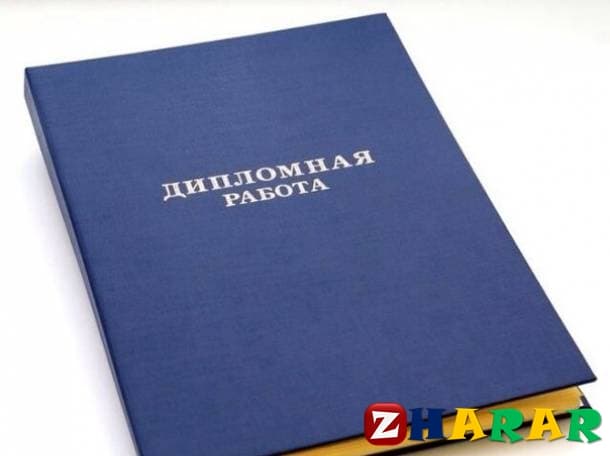
Содержание
Введение …………………………………………………………………………
1 Литературный обзор………………………………………………………….
2 Экспериментальная часть ................................................................................
2.1 Характеристика каучуков и ингредиентов .................................................. 2.2 Методы экспериментов и испытаний............................................................
2.4 Результаты экспериментов и заключения.....................................................
3. Технологическая часть ....................................................................................
3.1 Описание технологической схемы приготовления резиновых смесей .....
3.2 Разработка рецептур и приготовление резиновых смесей с использованием волластонитов Верхне-Бадамского месторождения ………
4 Материальный баланс ......................................................................................
5 Охрана окружающей среды ………………………………………………...
6 Охрана труда и техника безопасности ……………………………………...
7 Технико-экономические показатели процесса ……………………………..
8 Бизнес – план .....................................................................................................
9 Заключение.........................................................................................................
Список использованных источников ………………………………………….
Приложение.
Литературный обзор
1.1 Минеральные наполнители для резин
Одним из эффективных способов модификации свойств полимерных материалов является их наполнение – введение твердых или газообразных веществ – наполнителей, которые, равномерно распределяясь в объеме получающейся композиции, образуют четко выраженную границу раздела с полимерной средой. Введение наполнителей способствует улучшению физико-механических и технологических свойств полимеров, а также увеличению объема материала, т.е. снижению его стоимости /1-4/.
Действие наполнителя определяется множеством факторов – формой и размером частиц, особенностями взаимодействия с полимером, особенностями взаимодействия между частицами наполнителя в среде полимера, количеством наполнителя и другими, При введении наполнителей в полимер между полимером и наполнителем возможно адсорбционное, а в некоторых случаях и химическое взаимодействие на границе двух фаз. Это взаимодействие тем сильнее, чем больше поверхность контакта полимера с наполнителем, т.е. чем меньше размер частиц наполнителя и, соответственно, больше его суммарная поверхность. Адсорбционное и химическое взаимодействие на границе раздела фаз существенно зависят от природы полимера и наполнителя, от свойств поверхности наполнителя, наличия на ней низкомолекулярных веществ, а также от условий смешения полимера с наполнителем.
К неорганическим наполнителям относятся как минеральные наполнители природного происхождения – мел, каолин и другие, так и синтетические минеральные наполнители – коллоидная кремнекислота, оксиды и силикаты различных металлов.
С расширением производства синтетических каучуков возникла необходимость в применении усиливающих наполнителей, обеспечивающих высокую термостойкость, стойкость к различным агрессивным средам, негорючесть и другие свойства. Усиление каучуков заключается в том, что при введении тонкодисперсных наполнителей в резиновые смеси происходит существенное увеличение прочности и улучшение некоторых физико–механических свойств вулканизатов в высокоэластическом состоянии: сопротивления истиранию и раздиру, прочность при удлинении, твердость и т.п.
Минеральные наполнители природного происхождения, как ингредиенты резиновых смесей, с самого начала развития резиновой промышленности нашли широкое применение. Хотя они и изменяли физические свойства вулканизатов, придавая им ряд положительных свойств, но основной целью их применения было снижение стоимости резиновых изделий. Они также применялись для получения цветных резин на основе натурального каучука. Свойства некоторых минеральных наполнителей для резин приведены в таблице 1.
Таблица 1- Физико-химические свойства наполнителей
Показатель Наполнители
Мел Тальк Каолин
химический состав CaCO3 3MgO.4SiO2.H2O Al2O3.SiO2.H2O
цвет измельченного
материала
Белый
серый, белый
белый
Форма частиц зернистая чешуйчатая пластинчатая
поверхностные свойства
частиц гидрофильные гидрофильные гидрофильные
Плотность, кг/м3 2700-2900 2700-2800 2580
рН водной вытяжки 9,3 9,0-9,5 4,5
С расширением производства синтетических каучуков возникла необходимость в применении усиливающих наполнителей, обеспечивающих высокую термостойкость, стойкость к различным агрессивным средам, негорючесть и другие свойства. Усиление каучуков заключается в том, что при введении тонкодисперсных наполнителей в резиновые смеси происходит существенное увеличение прочности и улучшение некоторых физико–механических свойств вулканизатов в высокоэластическом состоянии: сопротивления истиранию и раздиру, прочность при удлинении, твердость и т.п. Важнейшим фактором, определяющим усиливающее действие наполнителей, является их дисперсность, характеризуемая размером частиц или удельной поверхностью. Подобным требованиям отвечают минеральные наполнители, такие как, например, мел и каолин. Резиновые смеси, наполненные мелом, легко каландрируются и шприцуются, имеют ровную поверхность, хорошо заполняют формы. При введении каолина повышаются прочность при удлинении, твердость и сопротивление истиранию вулканизатов. Кроме этого, каолины повышают диэлектрические показатели, масло- и бензостойкость, а также кислотостойкость резин. Природным минералом, обладающим свойствами и составом близким к каолину является цеолит /4-7/.
1.2 Модификация резин наполнителями
Понятие химической модификации полимеров чрезвычайно многогранно и она может быть определена следующим образом: ”Модификация – это направленное изменение свойств полимеров при введении в состав макромолекул малого количества фрагментов иной природы /5, 7/.
Химическая модификация резин позволяет существенно улучшить их физико-механические характеристики, повысить надежность, долговечность и ремонтопригодность изделий без использования новых типов эластомеров и ингредиентов резиновых смесей. Химическая модификация целесообразна и с точки зрения энергосбережения, так как позволяет обойтись без энергоемких производств новых каучуков, дает возможность снизить каучукосодержание резиновых смесей путем увеличения дозировок наполнителей, позволяет в некоторых случаях осуществить замену дорогих и труднодоступных ингредиентов резиновых смесей на дешевые и доступные природные минеральные соединения и существенно интенсифицирует технологические процессы производства шин и РТИ /8-12/.
Все методы химической модификации классифицируют следующим образом /4/:
1) модификация, основанная на химических превращениях уже синтезированных макромолекул при их взаимодействии как с низкомолекулярными соединениями, способными к процессам полимеризации в массе модифицируемого полимера, так и с реагентами, не подверженными данными явлениями;
2) модификация, основанная на взаимодействии полимера с высокомолекулярными соединениями;
3) модификация на стадии синтеза полимера.
Все эти методы широко используются при изготовлении различных материалов. Однако в технологии резины наибольшее значение имеют методы модификации эластомеров за счет введения в них в процессе переработки активных низкомолекулярных соединений, как правило, полифункционального характера. При взаимодействии эластомеров с этими соединениями или продуктами их распада в структуре макромолекул образуются новые функциональные группы. Такие функциональные группы, как и сами модификаторы, могут участвовать в процессах вулканизации, формировании вулканизационной сетки, создании определенных микрогетерогенных областей в вулканизатах, ингибировании окислительных процессов в каучуках и резинах, улучшении когезионных и адгезионных свойств сырых резиновых смесей и вулканизатов. Все это приводит к значительному повышению эксплуатационных характеристик изделий, приданию им новых свойств /12,13/.
В настоящее время накоплен большой экспериментальный материал по химической модификации эластомеров, сделаны попытки его обобщения /5/.
Механические и адгезионные свойства модифицированных резин. Различают три основных режима работы резиновых изделий: постоянной деформации (ε = const), постоянного напряжения (δ = const) и постоянной работы деформации (δε = const). При режиме постоянной деформации величина деформации не зависит от свойств материала, а возникающее напряжение прямо пропорционально модулю упругости. При этом режиме в более мягком материале развиваются меньшие напряжения, то есть он находится в более выгодных условиях. При режиме постоянного напряжения величина испытываемых резиной напряжений остается постоянной независимо от жесткости резины, а величина деформации изменяется обратно пропорционально модулю упругости материала. Следовательно, в режиме постоянного напряжения в более выгодных условиях находятся высокомодульные резины. Режим постоянной работы является промежуточным между режимами постоянного напряжения и постоянной деформации. При этом режиме независимо от упругих свойств резины работа деформации остается постоянной, а сами напряжения и деформации меняются так, чтобы сохранялось постоянным их произведение.
В связи с наличием в молекуле модификатора полярных функциональных групп плотность энергии когезии модификатора выше, чем у карбоцепных эластомеров, поэтому модификаторы малорастворимы или совсем нерастворимы в эластомерной матрице и диффундируют на ее поверхность. В связи с этим модификаторы влияют на поверхностное натяжение резиновой смеси и улучшают смачивание полярных субстратов.
Вследствие образования при химической модификации дополнительных связей эластомер – эластомер и эластомер – наполнитель существенно возрастают модули упругости резин. Чем значительнее повышение интенсивности межфазного взаимодействия на границе эластомер – наполнитель, тем больше эффект повышения упругожесткостных свойств резин при одной и той же эффективной концентрации поперечных связей. Благодаря этому истинный модификатор полифункционален по характеру своего влияния на свойства резин: степень диспергирования наполнителя, электросопротивление, содержание связанного эластомера, вязкость невулканизованной смеси, деформационные свойства (когезионную прочность) смесей, модуль упругости и твердость вулканизатов, прочностные свойства (сопротивление разрыву, раздиру, проколу, прорыву и т.п.), температуростойкость, износостойкость и др /13-27/.
В настоящее время перспективными минеральными наполнителями и модификатороми неорганического происхождения для эластомерных материалов является Коксуйские шунгиты, Верхне – Бадамские волластониты, Шанханайские цеолиты /27, 28/.
1.3 Волластонит - универсальный функциональный наполнитель
Волластонит - это природный силикат кальция с молекулярной формулой CaSiO3. Будучи известным как слоистый шпат с конца XVIII века, в 1822 году он был назван волластонитом в честь английского химика и философа Вильяма Хайда Волластона (William Hyde Wollaston). Однако переименование волластонита оставалось не более чем просто любопытным фактом вплоть до начала его первого промышленного использования в 1933 году, когда он начал добываться в Калифорнии в качестве сырья для производства минерального волокна. Волластонит не получил широкого промышленного распространения вплоть до 50-х годов XX века, когда, во время послевоенного строительного бума, он начал использоваться для производства красок, грунтовок, шпатлевок и керамики.
Волластонит уникален среди промышленных минералов благодаря сочетанию белого цвета, игольчатой формы кристаллов и щелочному pH. Промышленные сорта волластонита обычно обладают высокой степенью очистки, так как значительная часть побочных примесей извлекается в ходе влажной обработки и высокоинтенсивного магнитного разделения. Обычно сопутствующими волластониту минералами являются кварц, кальцит, диопсид, гранат и прегнит. Эти включения - результат естественного образования волластонита путем контактного метаморфизма кварца и известняка в соответствии со следующей формулой:
CaCO3 +
кальцит SiO2 <
кварц CaSiO3 +
волластонит CO2
диоксид углерода
Тепло, потребляемое реакцией волластонита, обеспечивается вулканической магмой, которая также вносит алюминий, магний и железо, образующие сопутствующие минералы.
Структура и свойства
Рисунок 1 показывает, что структура волластонита характеризуется повторяющимися, переплетенными тройными четырехгранниками кварца. Цепочки, формируемые этими кварцевыми четырехгранниками соединены по сторонам через кальций, образуя восьмигранники. Благодаря такой структуре, волластонит растет как игольчатый кристалл и сохраняет эту игольчатую структуру при расщеплении. Высокая плотность кварцевых цепочек обеспечивает твердость этого минерала (4,5-5 по Моосу). В природе небольшое количество кальция может замещаться железом, магнием, марганцем, алюминием, калием и натрием. Потери при прокаливании (летучие вещества, испаряющиеся при 1000 град. С) очень низки для чистого волластонита. У промышленных образцов потери при прокаливании варьируются в диапазоне 0.5%-2.0%, главным образом в зависимости от содержания остаточного кальцита.
Рисунок 1 – Структура волластонита
Поверхность волластонита при контакте с водой гидролизуется, образуя гидроксид кальция, который обеспечивает щелочность дисперсий волластонита. Волластонит разлагается минеральными кислотами, особенно соляной кислотой, и некоторыми органическими кислотами (муравьиной, уксусной, лимонной, молочной). При неполном разложении в кислотах образуется силикагель. Волластонит обладает сильным буферным эффектом в кислых растворах благодаря освобождению ионов кальция.
Сорта волластонита
Использование волластонита в наполнителях обусловлено в первую очередь величиной иголок в природных кристаллах волластонита, форма которых сохраняется при измельчении в конечные продукты. Анизотропия частиц волластонита описывается характеристическим отношением - отношением длины частиц к их ширине. Базовая классификация промышленных сортов волластонита основана на размере и форме частиц.
Получение промышленных сортов волластонита часто требует специальных усилий по удалению или снижению содержания нежелательных примесей. Руда вначале дробится и перемалывается для выделения минералов. Гранат и диопсид - окрашенные компоненты волластонитовой руды - обладают слабыми магнитными свойствами и могут быть удалены высокоинтенсивными магнитными сепараторами. Кальцит удаляется флотацией.
Волластонит измельчается преимущественно в шаровых мельницах. Порошковые сорта волластонита размалываются до относительно низкого характеристического отношения (3:1-5:1). Сорта с высоким характеристическим отношением получают осторожным перетиром с сохранением игольчатой структуры частиц. При необходимости воздушными сепараторами отделяется пылевидная фракция. Сорта с высоким характеристическим отношением имеют показатели от 12:1 до 20:1. Промышленный волластонит имеет среднюю длину иголок от 200 мкм для длиноразмерных до 20 мкм для микроигольчатых сортов. Рисунок 2 иллюстрирует структру микроигольчатого волластонита с высоким характеристическим отношением.
Рисунок 2 – Структура микроигольчатого волластонита
Как мелко-, так и крупноразмерные сорта волластонита доступны в силановой и органосилановой обработке для улучшения совместимости с органическими матрицами.
Эволюция как функционального наполнителя
Как функциональный наполнитель для лакокрасочных материалов волластонит стал применяться с середины 40-х годов XX века. Привлекательными свойствами этого минерала в данном приложении оказались его белый цвет, довольно высокая твердость и высокая естественная белизна.
В обзоре свойств и направлений применения волластонита, опубликованном в 1979 году, отмечалось, что важнейшими свойствами этого минерала как наполнителя ЛКМ на протяжении более 25 лет были придание покрытиям устойчивости к коррозии, поверхностной износостойкости, способности к сохранению цвета при атмосферных воздействиях. Статья описывала результаты исследования, сравнивающего волластонит с другими видами наполнителей в латексных красках как для наружных, так и для внутренних работ. Также отмечалось использование модифицированного волластонита в акриловых и алкидных красках, содержащих оксид цинка. При использовании 30-микронного волластонита цинковые белила были стабилизированы без применения большого количества диспергатора. Из преимуществ отмечались: снижение себестоимости продукции и высокая стабильность при хранении.
Автор статьи, после сравнения волластонита с другими видами функциональных наполнителей в ЛКМ, отмечает следующие его уникальные свойства:
Универсальность - основанная на игольчатой форме частиц, обеспечивающей матирующую способность, прочность в тонких покрытиях и общую стабильность;
Умеренную маслоемкость, подходящую для рецептур с высокой объемной концентрацией пигментов;
Высокую яркость, обеспечивающую более чистые оттенки;
Сравнительно высокую твердость, обеспечивающую стойкость к абразивному износу;
Щелочной показатель pH, который становится одним из важнейших свойств волластонита, поскольку обеспечивает снижение расхода аммиака и улучшает стойкость покрытий к коррозии и плесени.
Пять лет спустя, несколько наполнителей были исследованы на предмет обеспечения антикоррозийной стойкости эпоксидных грунтовок для металлических поверхностей. Поскольку применение свинцовых и хромовых ингибиторов коррозии было запрещено, то возникали новые виды ингибиторов: молибдатные, боратные и фосфатные. Но они имели свои недостатки, связанные с высокой маслоемкостью и низкой эффективностью. Изучение влияния соотношения ОКП / КОКП (объемная концентрация пигмента / критическая объемная концентрация пигмента) на сохранение антикоррозионных свойств грунтовок привело к пересмотру выбора наполнителя. Среди 9 сравниваемых наполнителей предпочтение было отдано волластониту, обеспечивающему наилучшие коррозионную стойкость и стойкость к вспучиванию. Эти показатели могли быть еще лучше при использовании волластонита, модифицированного эпоксиланом [3].
Совсем недавно была опубликована работа [4] по использованию волластонита, модифицированного реакционноспособными силанами с амино- и эпоксигруппами в коррозионностойких покрытиях. В этой статье описывалась роль волластонита как "синергиста" защитных пигментов-ингибиторов. Несмотря на то, что этот механизм еще недостаточно изучен, различные авторы отмечают хорошие результаты применения волластонита в сочетании с большинством основных ингибиторов коррозии. Известно, что совместное использование ингибиторов коррозии и волластонита, особенно его поверхностно-модифицированных марок, обеспечивает большую стойкость покрытий к коррозии, чем при использовании защитных пигментов отдельно, без волластонита. Один из авторов в исследовании [5], посвященном водно-эпоксидным грунтовкам и антикоррозийным пигментам, приходит к следующим заключениям касательно модифицированного волластонита и его свойств:
Величина ОКП в пределах 38-45% и соотношение ОКП/КОКП в интервале 0,6-0,9 обеспечивают наилучщие свойства покрытия при дозировках модифицированного волластонита 150 г/л и антикоррозионного пигмента 100 г/л;
Прекрасные покрывающие свойства;
Высокие показатели стойкости к длительному воздействию соляного тумана и влажности;
Величина ОКП на уровне 38% обеспечивает лучшую покрываемость и устойчивость к коррози....
Введение …………………………………………………………………………
1 Литературный обзор………………………………………………………….
2 Экспериментальная часть ................................................................................
2.1 Характеристика каучуков и ингредиентов .................................................. 2.2 Методы экспериментов и испытаний............................................................
2.4 Результаты экспериментов и заключения.....................................................
3. Технологическая часть ....................................................................................
3.1 Описание технологической схемы приготовления резиновых смесей .....
3.2 Разработка рецептур и приготовление резиновых смесей с использованием волластонитов Верхне-Бадамского месторождения ………
4 Материальный баланс ......................................................................................
5 Охрана окружающей среды ………………………………………………...
6 Охрана труда и техника безопасности ……………………………………...
7 Технико-экономические показатели процесса ……………………………..
8 Бизнес – план .....................................................................................................
9 Заключение.........................................................................................................
Список использованных источников ………………………………………….
Приложение.
Литературный обзор
1.1 Минеральные наполнители для резин
Одним из эффективных способов модификации свойств полимерных материалов является их наполнение – введение твердых или газообразных веществ – наполнителей, которые, равномерно распределяясь в объеме получающейся композиции, образуют четко выраженную границу раздела с полимерной средой. Введение наполнителей способствует улучшению физико-механических и технологических свойств полимеров, а также увеличению объема материала, т.е. снижению его стоимости /1-4/.
Действие наполнителя определяется множеством факторов – формой и размером частиц, особенностями взаимодействия с полимером, особенностями взаимодействия между частицами наполнителя в среде полимера, количеством наполнителя и другими, При введении наполнителей в полимер между полимером и наполнителем возможно адсорбционное, а в некоторых случаях и химическое взаимодействие на границе двух фаз. Это взаимодействие тем сильнее, чем больше поверхность контакта полимера с наполнителем, т.е. чем меньше размер частиц наполнителя и, соответственно, больше его суммарная поверхность. Адсорбционное и химическое взаимодействие на границе раздела фаз существенно зависят от природы полимера и наполнителя, от свойств поверхности наполнителя, наличия на ней низкомолекулярных веществ, а также от условий смешения полимера с наполнителем.
К неорганическим наполнителям относятся как минеральные наполнители природного происхождения – мел, каолин и другие, так и синтетические минеральные наполнители – коллоидная кремнекислота, оксиды и силикаты различных металлов.
С расширением производства синтетических каучуков возникла необходимость в применении усиливающих наполнителей, обеспечивающих высокую термостойкость, стойкость к различным агрессивным средам, негорючесть и другие свойства. Усиление каучуков заключается в том, что при введении тонкодисперсных наполнителей в резиновые смеси происходит существенное увеличение прочности и улучшение некоторых физико–механических свойств вулканизатов в высокоэластическом состоянии: сопротивления истиранию и раздиру, прочность при удлинении, твердость и т.п.
Минеральные наполнители природного происхождения, как ингредиенты резиновых смесей, с самого начала развития резиновой промышленности нашли широкое применение. Хотя они и изменяли физические свойства вулканизатов, придавая им ряд положительных свойств, но основной целью их применения было снижение стоимости резиновых изделий. Они также применялись для получения цветных резин на основе натурального каучука. Свойства некоторых минеральных наполнителей для резин приведены в таблице 1.
Таблица 1- Физико-химические свойства наполнителей
Показатель Наполнители
Мел Тальк Каолин
химический состав CaCO3 3MgO.4SiO2.H2O Al2O3.SiO2.H2O
цвет измельченного
материала
Белый
серый, белый
белый
Форма частиц зернистая чешуйчатая пластинчатая
поверхностные свойства
частиц гидрофильные гидрофильные гидрофильные
Плотность, кг/м3 2700-2900 2700-2800 2580
рН водной вытяжки 9,3 9,0-9,5 4,5
С расширением производства синтетических каучуков возникла необходимость в применении усиливающих наполнителей, обеспечивающих высокую термостойкость, стойкость к различным агрессивным средам, негорючесть и другие свойства. Усиление каучуков заключается в том, что при введении тонкодисперсных наполнителей в резиновые смеси происходит существенное увеличение прочности и улучшение некоторых физико–механических свойств вулканизатов в высокоэластическом состоянии: сопротивления истиранию и раздиру, прочность при удлинении, твердость и т.п. Важнейшим фактором, определяющим усиливающее действие наполнителей, является их дисперсность, характеризуемая размером частиц или удельной поверхностью. Подобным требованиям отвечают минеральные наполнители, такие как, например, мел и каолин. Резиновые смеси, наполненные мелом, легко каландрируются и шприцуются, имеют ровную поверхность, хорошо заполняют формы. При введении каолина повышаются прочность при удлинении, твердость и сопротивление истиранию вулканизатов. Кроме этого, каолины повышают диэлектрические показатели, масло- и бензостойкость, а также кислотостойкость резин. Природным минералом, обладающим свойствами и составом близким к каолину является цеолит /4-7/.
1.2 Модификация резин наполнителями
Понятие химической модификации полимеров чрезвычайно многогранно и она может быть определена следующим образом: ”Модификация – это направленное изменение свойств полимеров при введении в состав макромолекул малого количества фрагментов иной природы /5, 7/.
Химическая модификация резин позволяет существенно улучшить их физико-механические характеристики, повысить надежность, долговечность и ремонтопригодность изделий без использования новых типов эластомеров и ингредиентов резиновых смесей. Химическая модификация целесообразна и с точки зрения энергосбережения, так как позволяет обойтись без энергоемких производств новых каучуков, дает возможность снизить каучукосодержание резиновых смесей путем увеличения дозировок наполнителей, позволяет в некоторых случаях осуществить замену дорогих и труднодоступных ингредиентов резиновых смесей на дешевые и доступные природные минеральные соединения и существенно интенсифицирует технологические процессы производства шин и РТИ /8-12/.
Все методы химической модификации классифицируют следующим образом /4/:
1) модификация, основанная на химических превращениях уже синтезированных макромолекул при их взаимодействии как с низкомолекулярными соединениями, способными к процессам полимеризации в массе модифицируемого полимера, так и с реагентами, не подверженными данными явлениями;
2) модификация, основанная на взаимодействии полимера с высокомолекулярными соединениями;
3) модификация на стадии синтеза полимера.
Все эти методы широко используются при изготовлении различных материалов. Однако в технологии резины наибольшее значение имеют методы модификации эластомеров за счет введения в них в процессе переработки активных низкомолекулярных соединений, как правило, полифункционального характера. При взаимодействии эластомеров с этими соединениями или продуктами их распада в структуре макромолекул образуются новые функциональные группы. Такие функциональные группы, как и сами модификаторы, могут участвовать в процессах вулканизации, формировании вулканизационной сетки, создании определенных микрогетерогенных областей в вулканизатах, ингибировании окислительных процессов в каучуках и резинах, улучшении когезионных и адгезионных свойств сырых резиновых смесей и вулканизатов. Все это приводит к значительному повышению эксплуатационных характеристик изделий, приданию им новых свойств /12,13/.
В настоящее время накоплен большой экспериментальный материал по химической модификации эластомеров, сделаны попытки его обобщения /5/.
Механические и адгезионные свойства модифицированных резин. Различают три основных режима работы резиновых изделий: постоянной деформации (ε = const), постоянного напряжения (δ = const) и постоянной работы деформации (δε = const). При режиме постоянной деформации величина деформации не зависит от свойств материала, а возникающее напряжение прямо пропорционально модулю упругости. При этом режиме в более мягком материале развиваются меньшие напряжения, то есть он находится в более выгодных условиях. При режиме постоянного напряжения величина испытываемых резиной напряжений остается постоянной независимо от жесткости резины, а величина деформации изменяется обратно пропорционально модулю упругости материала. Следовательно, в режиме постоянного напряжения в более выгодных условиях находятся высокомодульные резины. Режим постоянной работы является промежуточным между режимами постоянного напряжения и постоянной деформации. При этом режиме независимо от упругих свойств резины работа деформации остается постоянной, а сами напряжения и деформации меняются так, чтобы сохранялось постоянным их произведение.
В связи с наличием в молекуле модификатора полярных функциональных групп плотность энергии когезии модификатора выше, чем у карбоцепных эластомеров, поэтому модификаторы малорастворимы или совсем нерастворимы в эластомерной матрице и диффундируют на ее поверхность. В связи с этим модификаторы влияют на поверхностное натяжение резиновой смеси и улучшают смачивание полярных субстратов.
Вследствие образования при химической модификации дополнительных связей эластомер – эластомер и эластомер – наполнитель существенно возрастают модули упругости резин. Чем значительнее повышение интенсивности межфазного взаимодействия на границе эластомер – наполнитель, тем больше эффект повышения упругожесткостных свойств резин при одной и той же эффективной концентрации поперечных связей. Благодаря этому истинный модификатор полифункционален по характеру своего влияния на свойства резин: степень диспергирования наполнителя, электросопротивление, содержание связанного эластомера, вязкость невулканизованной смеси, деформационные свойства (когезионную прочность) смесей, модуль упругости и твердость вулканизатов, прочностные свойства (сопротивление разрыву, раздиру, проколу, прорыву и т.п.), температуростойкость, износостойкость и др /13-27/.
В настоящее время перспективными минеральными наполнителями и модификатороми неорганического происхождения для эластомерных материалов является Коксуйские шунгиты, Верхне – Бадамские волластониты, Шанханайские цеолиты /27, 28/.
1.3 Волластонит - универсальный функциональный наполнитель
Волластонит - это природный силикат кальция с молекулярной формулой CaSiO3. Будучи известным как слоистый шпат с конца XVIII века, в 1822 году он был назван волластонитом в честь английского химика и философа Вильяма Хайда Волластона (William Hyde Wollaston). Однако переименование волластонита оставалось не более чем просто любопытным фактом вплоть до начала его первого промышленного использования в 1933 году, когда он начал добываться в Калифорнии в качестве сырья для производства минерального волокна. Волластонит не получил широкого промышленного распространения вплоть до 50-х годов XX века, когда, во время послевоенного строительного бума, он начал использоваться для производства красок, грунтовок, шпатлевок и керамики.
Волластонит уникален среди промышленных минералов благодаря сочетанию белого цвета, игольчатой формы кристаллов и щелочному pH. Промышленные сорта волластонита обычно обладают высокой степенью очистки, так как значительная часть побочных примесей извлекается в ходе влажной обработки и высокоинтенсивного магнитного разделения. Обычно сопутствующими волластониту минералами являются кварц, кальцит, диопсид, гранат и прегнит. Эти включения - результат естественного образования волластонита путем контактного метаморфизма кварца и известняка в соответствии со следующей формулой:
CaCO3 +
кальцит SiO2 <
кварц CaSiO3 +
волластонит CO2
диоксид углерода
Тепло, потребляемое реакцией волластонита, обеспечивается вулканической магмой, которая также вносит алюминий, магний и железо, образующие сопутствующие минералы.
Структура и свойства
Рисунок 1 показывает, что структура волластонита характеризуется повторяющимися, переплетенными тройными четырехгранниками кварца. Цепочки, формируемые этими кварцевыми четырехгранниками соединены по сторонам через кальций, образуя восьмигранники. Благодаря такой структуре, волластонит растет как игольчатый кристалл и сохраняет эту игольчатую структуру при расщеплении. Высокая плотность кварцевых цепочек обеспечивает твердость этого минерала (4,5-5 по Моосу). В природе небольшое количество кальция может замещаться железом, магнием, марганцем, алюминием, калием и натрием. Потери при прокаливании (летучие вещества, испаряющиеся при 1000 град. С) очень низки для чистого волластонита. У промышленных образцов потери при прокаливании варьируются в диапазоне 0.5%-2.0%, главным образом в зависимости от содержания остаточного кальцита.
Рисунок 1 – Структура волластонита
Поверхность волластонита при контакте с водой гидролизуется, образуя гидроксид кальция, который обеспечивает щелочность дисперсий волластонита. Волластонит разлагается минеральными кислотами, особенно соляной кислотой, и некоторыми органическими кислотами (муравьиной, уксусной, лимонной, молочной). При неполном разложении в кислотах образуется силикагель. Волластонит обладает сильным буферным эффектом в кислых растворах благодаря освобождению ионов кальция.
Сорта волластонита
Использование волластонита в наполнителях обусловлено в первую очередь величиной иголок в природных кристаллах волластонита, форма которых сохраняется при измельчении в конечные продукты. Анизотропия частиц волластонита описывается характеристическим отношением - отношением длины частиц к их ширине. Базовая классификация промышленных сортов волластонита основана на размере и форме частиц.
Получение промышленных сортов волластонита часто требует специальных усилий по удалению или снижению содержания нежелательных примесей. Руда вначале дробится и перемалывается для выделения минералов. Гранат и диопсид - окрашенные компоненты волластонитовой руды - обладают слабыми магнитными свойствами и могут быть удалены высокоинтенсивными магнитными сепараторами. Кальцит удаляется флотацией.
Волластонит измельчается преимущественно в шаровых мельницах. Порошковые сорта волластонита размалываются до относительно низкого характеристического отношения (3:1-5:1). Сорта с высоким характеристическим отношением получают осторожным перетиром с сохранением игольчатой структуры частиц. При необходимости воздушными сепараторами отделяется пылевидная фракция. Сорта с высоким характеристическим отношением имеют показатели от 12:1 до 20:1. Промышленный волластонит имеет среднюю длину иголок от 200 мкм для длиноразмерных до 20 мкм для микроигольчатых сортов. Рисунок 2 иллюстрирует структру микроигольчатого волластонита с высоким характеристическим отношением.
Рисунок 2 – Структура микроигольчатого волластонита
Как мелко-, так и крупноразмерные сорта волластонита доступны в силановой и органосилановой обработке для улучшения совместимости с органическими матрицами.
Эволюция как функционального наполнителя
Как функциональный наполнитель для лакокрасочных материалов волластонит стал применяться с середины 40-х годов XX века. Привлекательными свойствами этого минерала в данном приложении оказались его белый цвет, довольно высокая твердость и высокая естественная белизна.
В обзоре свойств и направлений применения волластонита, опубликованном в 1979 году, отмечалось, что важнейшими свойствами этого минерала как наполнителя ЛКМ на протяжении более 25 лет были придание покрытиям устойчивости к коррозии, поверхностной износостойкости, способности к сохранению цвета при атмосферных воздействиях. Статья описывала результаты исследования, сравнивающего волластонит с другими видами наполнителей в латексных красках как для наружных, так и для внутренних работ. Также отмечалось использование модифицированного волластонита в акриловых и алкидных красках, содержащих оксид цинка. При использовании 30-микронного волластонита цинковые белила были стабилизированы без применения большого количества диспергатора. Из преимуществ отмечались: снижение себестоимости продукции и высокая стабильность при хранении.
Автор статьи, после сравнения волластонита с другими видами функциональных наполнителей в ЛКМ, отмечает следующие его уникальные свойства:
Универсальность - основанная на игольчатой форме частиц, обеспечивающей матирующую способность, прочность в тонких покрытиях и общую стабильность;
Умеренную маслоемкость, подходящую для рецептур с высокой объемной концентрацией пигментов;
Высокую яркость, обеспечивающую более чистые оттенки;
Сравнительно высокую твердость, обеспечивающую стойкость к абразивному износу;
Щелочной показатель pH, который становится одним из важнейших свойств волластонита, поскольку обеспечивает снижение расхода аммиака и улучшает стойкость покрытий к коррозии и плесени.
Пять лет спустя, несколько наполнителей были исследованы на предмет обеспечения антикоррозийной стойкости эпоксидных грунтовок для металлических поверхностей. Поскольку применение свинцовых и хромовых ингибиторов коррозии было запрещено, то возникали новые виды ингибиторов: молибдатные, боратные и фосфатные. Но они имели свои недостатки, связанные с высокой маслоемкостью и низкой эффективностью. Изучение влияния соотношения ОКП / КОКП (объемная концентрация пигмента / критическая объемная концентрация пигмента) на сохранение антикоррозионных свойств грунтовок привело к пересмотру выбора наполнителя. Среди 9 сравниваемых наполнителей предпочтение было отдано волластониту, обеспечивающему наилучшие коррозионную стойкость и стойкость к вспучиванию. Эти показатели могли быть еще лучше при использовании волластонита, модифицированного эпоксиланом [3].
Совсем недавно была опубликована работа [4] по использованию волластонита, модифицированного реакционноспособными силанами с амино- и эпоксигруппами в коррозионностойких покрытиях. В этой статье описывалась роль волластонита как "синергиста" защитных пигментов-ингибиторов. Несмотря на то, что этот механизм еще недостаточно изучен, различные авторы отмечают хорошие результаты применения волластонита в сочетании с большинством основных ингибиторов коррозии. Известно, что совместное использование ингибиторов коррозии и волластонита, особенно его поверхностно-модифицированных марок, обеспечивает большую стойкость покрытий к коррозии, чем при использовании защитных пигментов отдельно, без волластонита. Один из авторов в исследовании [5], посвященном водно-эпоксидным грунтовкам и антикоррозийным пигментам, приходит к следующим заключениям касательно модифицированного волластонита и его свойств:
Величина ОКП в пределах 38-45% и соотношение ОКП/КОКП в интервале 0,6-0,9 обеспечивают наилучщие свойства покрытия при дозировках модифицированного волластонита 150 г/л и антикоррозионного пигмента 100 г/л;
Прекрасные покрывающие свойства;
Высокие показатели стойкости к длительному воздействию соляного тумана и влажности;
Величина ОКП на уровне 38% обеспечивает лучшую покрываемость и устойчивость к коррози....
Толық нұсқасын 30 секундтан кейін жүктей аласыз!!!
Әлеуметтік желілерде бөлісіңіз:
Facebook | VK | WhatsApp | Telegram | Twitter
Қарап көріңіз 👇
Пайдалы сілтемелер:
» Туған күнге 99 тілектер жинағы: өз сөзімен, қысқаша, қарапайым туған күнге тілек
» Абай Құнанбаев барлық өлеңдер жинағын жүктеу, оқу
» Дастархан батасы: дастарханға бата беру, ас қайыру
Соңғы жаңалықтар:
» 2025 жылы Ораза және Рамазан айы қай күні басталады?
» Утиль алым мөлшерлемесі өзгермейтін болды
» Жоғары оқу орындарына құжат қабылдау қашан басталады?