Автоматизация и управление вытяжкой оптического волокна
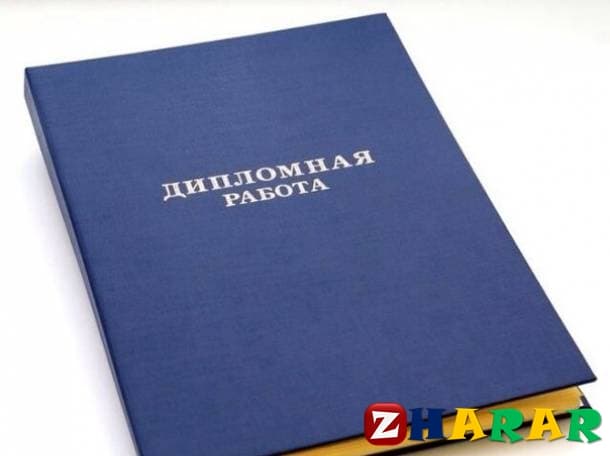
Содержание
Введение……………………………..……………………………………....6
1. Математическое моделирование технологического процесса вытяжки
оптического волокна ……………………………………………………………....8
1.1 Анализ известных методов, средств, способов организации
технологического процесса производства оптического волокна….8
1.2 Конструкция башни вытяжки оптических волокон ……………...14
1.2.1 Система подачи заготовки…………..……………………………15
1.2.2 Печь вытягивания ….……………………………………………..15
1.2.3 Датчик диаметра волокна ………………..……………………….16
1.2.4 Нанесение первичных покрытий ………………………………...17
1.2.5 Блок вытяжки ……………………………………………………..18
1.2.6 Намоточно-накопительное устройство ………………………….18
1.3 Экспериментальная идентификация объекта управления ……….19
1.3.1 Анализ процесса вытяжки ………………………………………..19
1.3.2 Математическая модель канала «скорость вытяжки –
диаметр»……………………………………………………………...22
1.3.3 Математическая модель канала «скорость подачи - диаметр
волокна»……………………………………………………………...24
1.3.4 Математические модели по каналам «температура – натяжение»,
«скорость подачи – натяжение», «скорость вытяжки —
натяжение» ……………..………………………………………..….26
1.3.5 Математическая модель по каналу «температура - диаметр
волокна»……………………………………………………………...28
1.4 Цифровая математическая модель ……………………..………….30
2. Управление процессом вытяжки оптического волокна из заготовки в
условиях высоких скоростей……………………………………………………..34
2.1 Анализ и синтез цифровой системы регулирования диаметром
волокна ………………………………………………………………34
2.2 Анализ и синтез системы автоматического управления в
пространстве состояний….…………………………………………41
2.3 Синтез системы с желаемым распределением корней
характеристического управления…………………..........................46
2.4 Система автоматического контроля положением заготовки ….....49
3. Техническая реализация адаптивной системы управления процессом
вытяжки оптического волокна из заготовки ………….……..………………....52
3.1 Общая схема системы автоматического управления процессом
вытяжки ……………………………………………………………..52
3.2 Система автоматической центровки заготовки ……………..…....55
3.3 Программирование приводов ……………………………………...58
3.4 Сервисные функции, выполняемые системой управления…….....61
4. Безопасность жизнедеятельности………………………………...…….63
4.1 Расчет освещения в помещении……………………………………63
4.2 Расчет искусственного освещения…………………………………66
8
4.3 Обеспечение безопасности от поражения электрическим током..69
5. Бизнес план…………………………………………………...………….74
5.1 Характеристика отрасли…………………….………………………74
5.2 Описание продукции и ее применение……………..……………...74
5.3 Анализ рынка………………………………………………………..75
5.4 Расчет затрат на разработку и внедрения системы автоматического
управления…………………...………………………………………75
5.5 Затраты на создание системы автоматизации……………………..77
5.6 Затраты на разработчиков программного продукта………………78
5.7 Затраты на приобретение приборов и средств автоматизации…...78
5.8 Вывод по экономической части………………………………….....80
Заключение ……………………………..…………….................................82
Список литературы ………………………………………………………..83
Приложение А…………………………………………………………………….88
Приложение Б…..…………………………………………………………………89
Приложение В…………………………………………………………………….90
Приложение Г……………………………………………………………………..92
Приложение Д…………………………………………………………………….93
Приложение Е……………………………………………………………………..94
Приложение Ж…………………………………………………………………….96
Приложение И…………………………………………………………………….99
1. Математическое моделирование технологического процесса
вытяжки оптического волокн
Технологический процесс изготовления оптического волокна, как
правило, состоит из двух этапов. Первый этап- получение заготовки, которая
представляет собой стеклянный стержень, обладающий волноводной
структурой, длиной порядка 1000 мм и диаметром 10 – 80 мм. На втором
этапе происходит вытяжка заготовки с нанесением защитного покрытия.
1.1 Анализ известных методов, средств, способов организации
технологического процесса производства оптического волокна
Методы, используемые для получения материала для оптических
волокон, можно разделить на две большие группы: тигельные или методы
осаждения из жидкой фазы и методы осаждения материала из газовой фазы. В
обоих случаях достижение малых потерь сопряжено с самым строгим
контролем чистоты исходных материалов и исключением попадания каких-
либо посторонних веществ в течение всего технологического процесса.
Обычно тигельные методы используют для изготовления волокон из
стекол с низкой температурой плавления. Тщательно очищенные и
измельченные компоненты помещают в платиновый или кварцевый тигель и
нагревают. При использовании для нагрева электрических печей компоненты
нагреваются за счет тепловой радиации от стенок печи, при этом последние не
должны содержать посторонних включений. Можно также использовать
нагрев компонент токами высокой частоты. При применении кварцевого
тигля необходимо порошкообразные компоненты стекла предварительно
подогреть и использовать более высокие частоты. В таком случае расплав
будет находиться при более высокой температуре, чем тигель, и,
следовательно, будет менее чувствителен к загрязнениям, попадающим в
расплав от стенок тигля. Следует отметить, что кварцевые тигли обычно не
используют более одного раза, поскольку они не выдерживают циклических
температурных воздействий. Традиционно стекло сердцевины получают в
виде цилиндрического стержня, а стекло оболочки в виде трубки, причем
цилиндр расположен внутри трубки, так что при совместном вытягивании и
получается оптическое волокно.
Одним из самых распространенных методов для изготовления
недорогих оптических волокон непрерывным способом, стал метод двойного
тигля. Метод двойного тигля характеризуется наличием двух концентрически
расположенных тиглей (рисунок 1.1). Материал центрального тигля служит
для образования сердцевины, а материал другого для создания оптической
оболочки. Вытяжка заготовки проводится вниз. Формирование сердцевины и
оболочки и их геометрических размеров происходит с помощью двух
концентрических фильер. Метод двойного тигля предпочтителен при
изготовлении ОВ со ступенчатым профилем показателя преломления.
Рисунок 1.1 - Метод вытяжки ОВ методом двойного тигля
Тигельный метод не подходит для изготовления кварцевых оптических
волокон, так как температура плавления стекол с большим содержанием
кремния оказывается слишком высокой для тигельного метода. Поэтому для
таких волокон должны применятся методы осаждения из газовой фазы.
Японскими учеными компании корпорации NTT во главе с Татсуо Изавой
(Tatsuo Izawa) был разработан метод осевого парофазного осаждения (VAD).
В основе метода лежит реакция окисления высокочистых газовых
компонентов (например, SiCl4, GeCl4), в результате которой образуются SiO2 и
GeO2. В горелку вместе с горючим газом подают смесь хлоридов и чистого
кислорода. В жарком пламени горелки (до 1600 °С) кремний и кислород
воссоединяются и рождаются мелкие порошкообразные частицы
высокочистого кварцевого стекла (SiO2), а «отделившийся» в
самостоятельный газ хлор улетучивается через вытяжной колпак. Поток
частиц кварцевого стекла направляется на вращающийся и перемещающийся
относительно горелки керамический стержень. Изменением концентрации
газовых добавок (GeCl4 и др.) можно изменять показатель преломления от
слоя к слою и получить необходимый профиль показателя преломления
заготовки.
Таким методом можно создавать заготовки, которых хватает на
несколько тысяч километров волокна, а в принципе процесс может быть
непрерывен - по мере изготовления заготовки из нее же можно вытягивать
волокно. На сегодняшний день это единственный метод позволяющий
осуществить производство непрерывного оптического волокна, так как
заготовка может быть сделана непрерывно бесконечной длины. Недостаток
этого метода заключается в трудном управлении пламенем для того, чтобы
сделать необходимый профиль и в трудностях в изготовлении волокна с
Рисунок 1.2 - Изготовление заготовки VAD-методом
Наиболее распространенным методом производства заготовок является
описанный в 1974 году американским физиком Джоном Макчеснеем
(JohnMacChesney) - метод химического парофазного осаждения (MCVD).
Изначально этот метод был открыт учеными компании Corning. При
использовании метода MCVD происходит осаждение сверхчистой двуокиси
кремния (при изготовлении сердцевины всегда добавляются определенные
примеси) на внутренней стороне стеклянной трубки, а затем - усаживание
трубки, вызываемое повышением температуры (с помощью пламени газа или
токов сверхвысокой частоты). В результате этого трубка сжимается и
превращается в сплошной стеклянный стержень диаметром 10-40 мм и длиной
около 1000 мм, обладающий волноводной структурой, такую же структуру
будет иметь и готовое волокно. Метод считается самым простым, и, кстати, в
отечественном производстве только он реально и работает
Рисунок 1.3 - Изготовление заготовки MCVD - методом
Однако для него нужна очень хорошая труба-заготовка без включений,
так как включения - это центры напряжений, из которых может начать расти
трещина. С этим довольно успешно борются путем химической или огневой
полировки поверхности трубок. Этот метод позволяет получать волокна с
малой величиной затухания, так как на всем протяжении процесса
изготовления каждого слоя сохраняется закрытое пространство, что позволяет
избежать примеси посторонних материалов. Метод достаточно универсален и
может применятся для изготовления одномодовых, градиентных волокон, а
также позволяет легко изменять показатель преломления слоя. Но
рассмотренный метод не позволяет сделать заготовку очень большой или
длинной и, соответственно, волокно не может быть сделано очень длинным, в
среднем от 3-5 км, с максимумом от 20 до 40 км. Диаметр заготовки
изготавливаемой таким способом не превышает 25 мм, для устранения этого
недостатка используется так называемый способ сверх покрытия. Разработано
устройство, позволяющее наносить сверх покрытие при одновременном
вытягивании. В проекте рассмотрено усовершенствование метода МСVD
путем замены газовой горелки на электропечь. Использование электропечи
позволяет уменьшить потери массы кварца, особенно при сжатии трубы в
стержень, получить лучшие геометрические параметры заготовок (при
условии контроля скорости при перемещении печи и давления в опорной
трубе).
Окисление кремния и хлористых германиев может также быть
инициировано плазмой. Метод названный позже PCVD-метод осаждения из
газовой фазы полученной путем плазменного распыления. Данный метод
впервые был разработан фирмой Philips. Поскольку зона образования газа
быстро перемещаться по трубке, в короткий отрезок времени возможно
нанести большое количество тонких слоев, производя в результате
однородные профили без видимых границ перехода от слоя к слою.
Фирмой Corning был разработан и запатентован ещё один метод - метод
внешнего парофазного осаждения(ОVD). Стекло осаждается на огнеупорный
стержень прямо из пламени горелки, куда подаются хлориды исходных
веществ. Поскольку осаждение происходит в атмосфере пламени, в таком
материале остается много воды, получившейся в результате окисления
водорода. Поэтому, после того как центральный стержень вынимают,
приходится продувать заготовку хлором, который экстрагирует воду. И
только после этого заготовка остекловывается. Перечисленные выше три фазы
процесса, а именно - осаждение на огнеупорный стержень, сушка и
остекловывание, происходят последовательно. Поэтому каждая фаза может
быть оптимизирована отдельно, что позволяет достичь высокой скорости
осаждения материала.
Данный метод позволяет получать стержень заготовки большой
непрерывной длины, например, 50-100 км и пригоден для производства всех
искусственных волокон. При использовании этого метода необходимо, чтобы
было подготовлено чистое пространство, которое охватывает все
пространство реакции или оборудования, так как все химические реакции
происходят на открытой площади.
Рисунок 1.4 - Изготовление заготовки а) методом OVD б) с последующей
сушкой в) спеканием
При соответствующей оптимизации процесса сушки, этот метод также
может использоваться для того, чтобы производить волокна с малыми
потерями, сопоставимыми по качеству с полученными внутренним
осаждением трубки.
На сегодняшний день все процессы получения заготовок путем
осаждения из газовой фазы являются сегодня двухэтапными. На первом этапе
производится так называемая заготовка - сердечник. Из заготовки -
сердечника, в зависимости от ее размера, может быть получено несколько
стержней, на которые потом наращивается оболочка. Затем заготовка с
наложенной оболочкой вытягивается в волокно. Различают несколько
различных способов изготовления такой оболочки: жакетирование, соль-гель,
плазма, кварцевый порошок.
Способ жакетирования представляет собой обжимание кремнеземной
трубки вокруг заготовки сердечника; это самый популярный процесс для
изготовления оболочки сердечников, полученных способами MCVD и PCVD.
Однако надеваемые наружные трубки весьма дороги. Поэтому компании, -
Alcatel и Lucent - организовали - в качестве альтернативы жакетированию -
серийное производство с получением оболочки волокна путем плазменного
распыления и с помощью соль-геля. Все производители сердечников волокна,
пользующиеся процессами OVD и VAD получают оболочку волокна с
помощью кварцевого порошка. Альтернатива жакетным трубам - кварцевые
цилиндры для RIC-технологии (Rod-In-Cylinder) вытяжки волокна. В RIC-
технологии жакетная труба заменяется полым цилиндром с внешним
диаметром от 120 до 200 мм. При этом процесс вытяжки волокна может быть
осуществлён двумя способами: непосредственно из стержневой заготовки и
жакетного цилиндра (Online RIC) или из предварительно изготовленной из
них кварцевой заготовки (Offline RIC).
В RIC-технологии может быть использована стержневая заготовка,
произведённая любым из существующих методов: MCVD, PCVD, VAD или
OVD.
В работе рассмотрен золь-гелевый метод изготовления заготовки. Золь-
гель процесс производства оптических заготовок разрабатывается с 1977 г. и
еще не имеет коммерческого применения. Существуют два основных метода
изготовления кварцевого гель-стекла: гидролиз и полимеризация алкоголятов;
превращение в гель золей, полученных из коллоидных оксидных дисперсий. С
помощью золь-гель процесса изготовляют опорную кварцевую трубу,
сердцевину и оптическую оболочку. Алкоголяты позволяют получать
многокомпонентные гели, и благодаря маленьким порам (2-7 нм), эти гели
могут спекаться при температурах, значительно меньших, чем температуры,
которые применяются при образовании стекла. Таким образом, можно
исключить проблему кристаллизации, так как спекание происходит при
температуре значительно ниже той, при которой начинается образование
центров кристаллизации и рост кристаллов. Однако сушка монолитных
алкоголятных гелей представляется трудной задачей. Она может быть решена
путем гиперкритической откачки воздуха из автоклава. Метод очень
трудоемок, требует громоздкого оборудования и больших затрат.
Приведенный обзор методов и средств изготовления заготовок
показывает, что наиболее перспективными являются методы осаждения из
газовой фазы.
Полученная любым из рассмотренных методов изготовления заготовка
вытягивается в волокно на специальных установках, которые в основном
отличаются способом нагрева заготовки в зоне формования. При этом
используются электропечи, кислородно-водородные горелки, индукционный
и лазерный метод нагрева.
На стадии вытяжки оптического волокна формируются два важнейших
параметра оптического волокна: предел прочности на растяжение и
коэффициент оптических потерь.
В процессе вытяжки световода конец заготовки нагревается в печи до
пластического состояния, при котором вязкость составляет 104-106 пуаз, при
этом тянущее устройство вытягивает высоковязкий расплав в тонкую нить.
Получение высококачественных оптических волокон возможно только при
тщательном контроле технологических параметров производства и
адекватной работе автоматических систем .....
Введение……………………………..……………………………………....6
1. Математическое моделирование технологического процесса вытяжки
оптического волокна ……………………………………………………………....8
1.1 Анализ известных методов, средств, способов организации
технологического процесса производства оптического волокна….8
1.2 Конструкция башни вытяжки оптических волокон ……………...14
1.2.1 Система подачи заготовки…………..……………………………15
1.2.2 Печь вытягивания ….……………………………………………..15
1.2.3 Датчик диаметра волокна ………………..……………………….16
1.2.4 Нанесение первичных покрытий ………………………………...17
1.2.5 Блок вытяжки ……………………………………………………..18
1.2.6 Намоточно-накопительное устройство ………………………….18
1.3 Экспериментальная идентификация объекта управления ……….19
1.3.1 Анализ процесса вытяжки ………………………………………..19
1.3.2 Математическая модель канала «скорость вытяжки –
диаметр»……………………………………………………………...22
1.3.3 Математическая модель канала «скорость подачи - диаметр
волокна»……………………………………………………………...24
1.3.4 Математические модели по каналам «температура – натяжение»,
«скорость подачи – натяжение», «скорость вытяжки —
натяжение» ……………..………………………………………..….26
1.3.5 Математическая модель по каналу «температура - диаметр
волокна»……………………………………………………………...28
1.4 Цифровая математическая модель ……………………..………….30
2. Управление процессом вытяжки оптического волокна из заготовки в
условиях высоких скоростей……………………………………………………..34
2.1 Анализ и синтез цифровой системы регулирования диаметром
волокна ………………………………………………………………34
2.2 Анализ и синтез системы автоматического управления в
пространстве состояний….…………………………………………41
2.3 Синтез системы с желаемым распределением корней
характеристического управления…………………..........................46
2.4 Система автоматического контроля положением заготовки ….....49
3. Техническая реализация адаптивной системы управления процессом
вытяжки оптического волокна из заготовки ………….……..………………....52
3.1 Общая схема системы автоматического управления процессом
вытяжки ……………………………………………………………..52
3.2 Система автоматической центровки заготовки ……………..…....55
3.3 Программирование приводов ……………………………………...58
3.4 Сервисные функции, выполняемые системой управления…….....61
4. Безопасность жизнедеятельности………………………………...…….63
4.1 Расчет освещения в помещении……………………………………63
4.2 Расчет искусственного освещения…………………………………66
8
4.3 Обеспечение безопасности от поражения электрическим током..69
5. Бизнес план…………………………………………………...………….74
5.1 Характеристика отрасли…………………….………………………74
5.2 Описание продукции и ее применение……………..……………...74
5.3 Анализ рынка………………………………………………………..75
5.4 Расчет затрат на разработку и внедрения системы автоматического
управления…………………...………………………………………75
5.5 Затраты на создание системы автоматизации……………………..77
5.6 Затраты на разработчиков программного продукта………………78
5.7 Затраты на приобретение приборов и средств автоматизации…...78
5.8 Вывод по экономической части………………………………….....80
Заключение ……………………………..…………….................................82
Список литературы ………………………………………………………..83
Приложение А…………………………………………………………………….88
Приложение Б…..…………………………………………………………………89
Приложение В…………………………………………………………………….90
Приложение Г……………………………………………………………………..92
Приложение Д…………………………………………………………………….93
Приложение Е……………………………………………………………………..94
Приложение Ж…………………………………………………………………….96
Приложение И…………………………………………………………………….99
1. Математическое моделирование технологического процесса
вытяжки оптического волокн
Технологический процесс изготовления оптического волокна, как
правило, состоит из двух этапов. Первый этап- получение заготовки, которая
представляет собой стеклянный стержень, обладающий волноводной
структурой, длиной порядка 1000 мм и диаметром 10 – 80 мм. На втором
этапе происходит вытяжка заготовки с нанесением защитного покрытия.
1.1 Анализ известных методов, средств, способов организации
технологического процесса производства оптического волокна
Методы, используемые для получения материала для оптических
волокон, можно разделить на две большие группы: тигельные или методы
осаждения из жидкой фазы и методы осаждения материала из газовой фазы. В
обоих случаях достижение малых потерь сопряжено с самым строгим
контролем чистоты исходных материалов и исключением попадания каких-
либо посторонних веществ в течение всего технологического процесса.
Обычно тигельные методы используют для изготовления волокон из
стекол с низкой температурой плавления. Тщательно очищенные и
измельченные компоненты помещают в платиновый или кварцевый тигель и
нагревают. При использовании для нагрева электрических печей компоненты
нагреваются за счет тепловой радиации от стенок печи, при этом последние не
должны содержать посторонних включений. Можно также использовать
нагрев компонент токами высокой частоты. При применении кварцевого
тигля необходимо порошкообразные компоненты стекла предварительно
подогреть и использовать более высокие частоты. В таком случае расплав
будет находиться при более высокой температуре, чем тигель, и,
следовательно, будет менее чувствителен к загрязнениям, попадающим в
расплав от стенок тигля. Следует отметить, что кварцевые тигли обычно не
используют более одного раза, поскольку они не выдерживают циклических
температурных воздействий. Традиционно стекло сердцевины получают в
виде цилиндрического стержня, а стекло оболочки в виде трубки, причем
цилиндр расположен внутри трубки, так что при совместном вытягивании и
получается оптическое волокно.
Одним из самых распространенных методов для изготовления
недорогих оптических волокон непрерывным способом, стал метод двойного
тигля. Метод двойного тигля характеризуется наличием двух концентрически
расположенных тиглей (рисунок 1.1). Материал центрального тигля служит
для образования сердцевины, а материал другого для создания оптической
оболочки. Вытяжка заготовки проводится вниз. Формирование сердцевины и
оболочки и их геометрических размеров происходит с помощью двух
концентрических фильер. Метод двойного тигля предпочтителен при
изготовлении ОВ со ступенчатым профилем показателя преломления.
Рисунок 1.1 - Метод вытяжки ОВ методом двойного тигля
Тигельный метод не подходит для изготовления кварцевых оптических
волокон, так как температура плавления стекол с большим содержанием
кремния оказывается слишком высокой для тигельного метода. Поэтому для
таких волокон должны применятся методы осаждения из газовой фазы.
Японскими учеными компании корпорации NTT во главе с Татсуо Изавой
(Tatsuo Izawa) был разработан метод осевого парофазного осаждения (VAD).
В основе метода лежит реакция окисления высокочистых газовых
компонентов (например, SiCl4, GeCl4), в результате которой образуются SiO2 и
GeO2. В горелку вместе с горючим газом подают смесь хлоридов и чистого
кислорода. В жарком пламени горелки (до 1600 °С) кремний и кислород
воссоединяются и рождаются мелкие порошкообразные частицы
высокочистого кварцевого стекла (SiO2), а «отделившийся» в
самостоятельный газ хлор улетучивается через вытяжной колпак. Поток
частиц кварцевого стекла направляется на вращающийся и перемещающийся
относительно горелки керамический стержень. Изменением концентрации
газовых добавок (GeCl4 и др.) можно изменять показатель преломления от
слоя к слою и получить необходимый профиль показателя преломления
заготовки.
Таким методом можно создавать заготовки, которых хватает на
несколько тысяч километров волокна, а в принципе процесс может быть
непрерывен - по мере изготовления заготовки из нее же можно вытягивать
волокно. На сегодняшний день это единственный метод позволяющий
осуществить производство непрерывного оптического волокна, так как
заготовка может быть сделана непрерывно бесконечной длины. Недостаток
этого метода заключается в трудном управлении пламенем для того, чтобы
сделать необходимый профиль и в трудностях в изготовлении волокна с
Рисунок 1.2 - Изготовление заготовки VAD-методом
Наиболее распространенным методом производства заготовок является
описанный в 1974 году американским физиком Джоном Макчеснеем
(JohnMacChesney) - метод химического парофазного осаждения (MCVD).
Изначально этот метод был открыт учеными компании Corning. При
использовании метода MCVD происходит осаждение сверхчистой двуокиси
кремния (при изготовлении сердцевины всегда добавляются определенные
примеси) на внутренней стороне стеклянной трубки, а затем - усаживание
трубки, вызываемое повышением температуры (с помощью пламени газа или
токов сверхвысокой частоты). В результате этого трубка сжимается и
превращается в сплошной стеклянный стержень диаметром 10-40 мм и длиной
около 1000 мм, обладающий волноводной структурой, такую же структуру
будет иметь и готовое волокно. Метод считается самым простым, и, кстати, в
отечественном производстве только он реально и работает
Рисунок 1.3 - Изготовление заготовки MCVD - методом
Однако для него нужна очень хорошая труба-заготовка без включений,
так как включения - это центры напряжений, из которых может начать расти
трещина. С этим довольно успешно борются путем химической или огневой
полировки поверхности трубок. Этот метод позволяет получать волокна с
малой величиной затухания, так как на всем протяжении процесса
изготовления каждого слоя сохраняется закрытое пространство, что позволяет
избежать примеси посторонних материалов. Метод достаточно универсален и
может применятся для изготовления одномодовых, градиентных волокон, а
также позволяет легко изменять показатель преломления слоя. Но
рассмотренный метод не позволяет сделать заготовку очень большой или
длинной и, соответственно, волокно не может быть сделано очень длинным, в
среднем от 3-5 км, с максимумом от 20 до 40 км. Диаметр заготовки
изготавливаемой таким способом не превышает 25 мм, для устранения этого
недостатка используется так называемый способ сверх покрытия. Разработано
устройство, позволяющее наносить сверх покрытие при одновременном
вытягивании. В проекте рассмотрено усовершенствование метода МСVD
путем замены газовой горелки на электропечь. Использование электропечи
позволяет уменьшить потери массы кварца, особенно при сжатии трубы в
стержень, получить лучшие геометрические параметры заготовок (при
условии контроля скорости при перемещении печи и давления в опорной
трубе).
Окисление кремния и хлористых германиев может также быть
инициировано плазмой. Метод названный позже PCVD-метод осаждения из
газовой фазы полученной путем плазменного распыления. Данный метод
впервые был разработан фирмой Philips. Поскольку зона образования газа
быстро перемещаться по трубке, в короткий отрезок времени возможно
нанести большое количество тонких слоев, производя в результате
однородные профили без видимых границ перехода от слоя к слою.
Фирмой Corning был разработан и запатентован ещё один метод - метод
внешнего парофазного осаждения(ОVD). Стекло осаждается на огнеупорный
стержень прямо из пламени горелки, куда подаются хлориды исходных
веществ. Поскольку осаждение происходит в атмосфере пламени, в таком
материале остается много воды, получившейся в результате окисления
водорода. Поэтому, после того как центральный стержень вынимают,
приходится продувать заготовку хлором, который экстрагирует воду. И
только после этого заготовка остекловывается. Перечисленные выше три фазы
процесса, а именно - осаждение на огнеупорный стержень, сушка и
остекловывание, происходят последовательно. Поэтому каждая фаза может
быть оптимизирована отдельно, что позволяет достичь высокой скорости
осаждения материала.
Данный метод позволяет получать стержень заготовки большой
непрерывной длины, например, 50-100 км и пригоден для производства всех
искусственных волокон. При использовании этого метода необходимо, чтобы
было подготовлено чистое пространство, которое охватывает все
пространство реакции или оборудования, так как все химические реакции
происходят на открытой площади.
Рисунок 1.4 - Изготовление заготовки а) методом OVD б) с последующей
сушкой в) спеканием
При соответствующей оптимизации процесса сушки, этот метод также
может использоваться для того, чтобы производить волокна с малыми
потерями, сопоставимыми по качеству с полученными внутренним
осаждением трубки.
На сегодняшний день все процессы получения заготовок путем
осаждения из газовой фазы являются сегодня двухэтапными. На первом этапе
производится так называемая заготовка - сердечник. Из заготовки -
сердечника, в зависимости от ее размера, может быть получено несколько
стержней, на которые потом наращивается оболочка. Затем заготовка с
наложенной оболочкой вытягивается в волокно. Различают несколько
различных способов изготовления такой оболочки: жакетирование, соль-гель,
плазма, кварцевый порошок.
Способ жакетирования представляет собой обжимание кремнеземной
трубки вокруг заготовки сердечника; это самый популярный процесс для
изготовления оболочки сердечников, полученных способами MCVD и PCVD.
Однако надеваемые наружные трубки весьма дороги. Поэтому компании, -
Alcatel и Lucent - организовали - в качестве альтернативы жакетированию -
серийное производство с получением оболочки волокна путем плазменного
распыления и с помощью соль-геля. Все производители сердечников волокна,
пользующиеся процессами OVD и VAD получают оболочку волокна с
помощью кварцевого порошка. Альтернатива жакетным трубам - кварцевые
цилиндры для RIC-технологии (Rod-In-Cylinder) вытяжки волокна. В RIC-
технологии жакетная труба заменяется полым цилиндром с внешним
диаметром от 120 до 200 мм. При этом процесс вытяжки волокна может быть
осуществлён двумя способами: непосредственно из стержневой заготовки и
жакетного цилиндра (Online RIC) или из предварительно изготовленной из
них кварцевой заготовки (Offline RIC).
В RIC-технологии может быть использована стержневая заготовка,
произведённая любым из существующих методов: MCVD, PCVD, VAD или
OVD.
В работе рассмотрен золь-гелевый метод изготовления заготовки. Золь-
гель процесс производства оптических заготовок разрабатывается с 1977 г. и
еще не имеет коммерческого применения. Существуют два основных метода
изготовления кварцевого гель-стекла: гидролиз и полимеризация алкоголятов;
превращение в гель золей, полученных из коллоидных оксидных дисперсий. С
помощью золь-гель процесса изготовляют опорную кварцевую трубу,
сердцевину и оптическую оболочку. Алкоголяты позволяют получать
многокомпонентные гели, и благодаря маленьким порам (2-7 нм), эти гели
могут спекаться при температурах, значительно меньших, чем температуры,
которые применяются при образовании стекла. Таким образом, можно
исключить проблему кристаллизации, так как спекание происходит при
температуре значительно ниже той, при которой начинается образование
центров кристаллизации и рост кристаллов. Однако сушка монолитных
алкоголятных гелей представляется трудной задачей. Она может быть решена
путем гиперкритической откачки воздуха из автоклава. Метод очень
трудоемок, требует громоздкого оборудования и больших затрат.
Приведенный обзор методов и средств изготовления заготовок
показывает, что наиболее перспективными являются методы осаждения из
газовой фазы.
Полученная любым из рассмотренных методов изготовления заготовка
вытягивается в волокно на специальных установках, которые в основном
отличаются способом нагрева заготовки в зоне формования. При этом
используются электропечи, кислородно-водородные горелки, индукционный
и лазерный метод нагрева.
На стадии вытяжки оптического волокна формируются два важнейших
параметра оптического волокна: предел прочности на растяжение и
коэффициент оптических потерь.
В процессе вытяжки световода конец заготовки нагревается в печи до
пластического состояния, при котором вязкость составляет 104-106 пуаз, при
этом тянущее устройство вытягивает высоковязкий расплав в тонкую нить.
Получение высококачественных оптических волокон возможно только при
тщательном контроле технологических параметров производства и
адекватной работе автоматических систем .....
Толық нұсқасын 30 секундтан кейін жүктей аласыз!!!
Әлеуметтік желілерде бөлісіңіз:
Facebook | VK | WhatsApp | Telegram | Twitter
Қарап көріңіз 👇
Пайдалы сілтемелер:
» Туған күнге 99 тілектер жинағы: өз сөзімен, қысқаша, қарапайым туған күнге тілек
» Абай Құнанбаев барлық өлеңдер жинағын жүктеу, оқу
» Дастархан батасы: дастарханға бата беру, ас қайыру
Соңғы жаңалықтар:
» 2025 жылы Ораза және Рамазан айы қай күні басталады?
» Утиль алым мөлшерлемесі өзгермейтін болды
» Жоғары оқу орындарына құжат қабылдау қашан басталады?