Разработка SCADA-системы узла смешения нефти нефтеналивного терминала
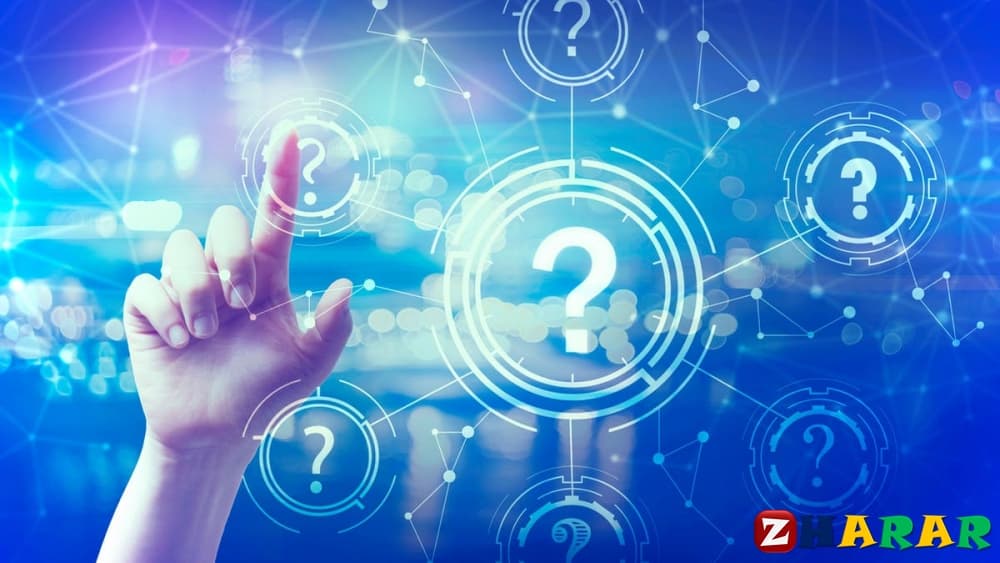
Содержание
Введение
1 Описание технологического объекта, и сравнительный анализ систем
его автоматизации
1.1 Назначения и производственная программа терминала
1.2 Функциональное описание терминала
1.3 Технологическое, функциональное описание узла (участка)
смешения нефти
1.4 Подходы разработки АСУ узла смешения нефти и структура
управления
1.5 Сравнительных анализ различных систем автоматизации
1.6 Цель дипломного проекта
2 Рассмотрение структуры производственного процесса и разработка
функциональной схемы автоматизации узла смешения нефти
2.1 Макроанализ
2.2 Микроанализ
2.3 Построение функциональной схемы автоматизации. Спецификация
электрических, электронных и электронно-механических устройств
автоматической системы управления
2.4 Синтез комплекса технических средств
3 Визуализация экрана АРМ оператора в SCADA системе Trace Modе
3.1 Выбор режима управления
3.2 Задание технологических параметров
3.3 Задание параметров работы оборудования
3.4 Условия пуска оборудования
3.5 Пуск оборудования
3.6 Процесс работы оборудования
3.7 Автоматическая остановка работы оборудования (окончание
производства)
3.8 Аварийная остановка работы оборудования оператором
(аварийное прерывание производства)
3.9 Сообщение об аварии
3.10 Контроль работы оборудования
3.11 Ручной режим управления.
4 Безопасность жизнедеятельности
4.1 Анализ условий труда при эксплуатации узла смешения нефти
4.2 Расчет защитного зануления оборудования
4.3 Расчет эффективности акустической виброизоляции насоса смешения
нефти
5.Экономическая часть. Экономическая эффективность автоматизации
узла смешения нефти.
5.1 Технологическое описание процесса
5.2 Определение затрат в системах автоматизации
5.3 Определение затрат на оборудование
Заключение
Список принятых сокращений
Список литературы
Приложение А Функциональная схема автоматизации
1 Описание технологического объекта, и сравнительный анализ
систем его автоматизации
1.1 Назначения и производственная программа терминала
Нефть из месторождения железнодорожным транспортом поступает на
одностороннюю сливно – наливную эстакаду, сливается в резервуар хранения
нефти. Далее производится дополнительная подготовка нефти на установке
компаундирования (смешения), после чего нефть отправляется железно-
дорожным транспортом до конечных потребителей. Компаундирование
проводится с целью получения нефти на заданную плотность, определенного
сорта.
Производственная программа терминала предусматривает
строительство пускового комплекса нефтеналивного терминала с
грузооборотом 300 тыс. тонн в год на базе существующей нефтебазы.
Проектируемое предприятие (терминал) предусматривает выполнение
следующих операций:
- прием, хранение и отгрузку железнодорожным транспортом светлых
нефтепродуктов в объеме 110 тыс. тонн/год, в том числе бензина - 20 тыс.
тонн/год, дизельного топлива - 90 тыс.тонн/год;
- прием, хранение и отгрузку железнодорожным транспортом темных
нефтепродуктов в объеме 70 тыс. тонн/год, в том числе мазута М-100 в объеме
40 тыс. тонн/год, печного топлива – 30 тыс. тонн/год;
- прием, хранение и отгрузку железнодорожным транспортом нефти в
объеме 120 тыс. тонн в год;
- подготовку (смешение) нефти в объеме 120 тыс. тонн в год, с учетом
возможного увеличения до 200 тыс. тонн/год.
В данном дипломном проекте рассматривается именно смешение
нефти, как отдельный участок этого технологического процесса.
1.2 Функциональное описание терминала
Для обеспечения производственной программы и приведения
производства в соответствие нормам и правилам проектом предусматривается
следующая схема работы нефтеналивного терминала (см. рисунок 1.1).
а) Прием вагоноцистерн с бензином и дизельным топливом на
одностороннюю сливно-наливную ж/д эстакаду на 10 вагоноцистерн.
Предусмотрена возможность операции слива (налива) светлых
нефтепродуктов одновременно с двух вагоноцистерн.б) Прием вагоноцистерн
с мазутом или вязкой нефтью на туже одностороннюю сливно-наливную ж/д
эстакаду на 10 вагоноцистерны.
Рисунок 1.1 – Схема технологических операций терминала
Предусмотрена возможность операции слива (налива) разогретого
мазута или вязкой нефти с двух вагоноцистерн (цистерны оборудованы
паровой рубашкой).
в) Прием вагоноцистерн с легкой нефтью на туже одностороннюю
сливо-наливную ж/д эстакаду на 10 вагоноцистерн. Предусмотрена
возможность операции слива (налива) легкой нефти одновременно с шести
вагоноцистерн.
г) Прием вагонорцистерн с печным топливом на туже одностороннюю
сливо-наливную ж/д эстакаду на 10 вагоноцистерн. Предусмотрена
возможность операции слива (налива) печного топлива одновременно двух
вагоноцистерн, согласно графику приема-отпуска. Прием печного топлива
после отгрузки мазута предусматривает зачистку труб и оборудования. Прием
мазута и печного топлива происходит поочередно.
д) Хранение бензина в проектируемом резервуарном парке РВС – 5000
3
ж) Хранение дизельного топлива в проектируемом резервуарном парке
РВС- 5000 м3.
з) Хранение печного топлива в проектируемом резервуарном парке РВС
- 10000м3.
и) Хранение нефти в проектируемом резервуарном парке РВС - 10000
3
к) Перекачка нефти и нефтепродуктов с ж/д эстакад в резервуарные
парки при помощи насосов.
л) Отгрузка нефти и нефтепродуктов на ж/д эстакаду при помощи
насосов.
м) Внутрибазовые перекачки нефти и нефтепродуктов.
н) Товарная подготовка нефти в узле смешения.
п)Анализ нефтепродуктов в химической лаборатории.
1.4 Технологическое, функциональное описание узла (участка)
смешения нефти
Смешение в нефтеперерабатывающей промышленности используется на
разных стадиях переработки, для получения автомобильных бензинов
используют 10-15 компонентов.
Смешение осуществляется на специальных установках, используя
циркуляционный способ – приготовление производится в смесительных
резервуарах, смешение в аппаратах с перемешивающими устройствами либо
непосредственное смешение в трубопроводах.
Разработке узла приготовления товарной продукции должен
предшествовать расчет ожидаемых показателей качества товарных продуктов
на основе сведений о качестве отдельных компонентов.
Способ приготовления товарной продукции циркуляцией через
смесительные резервуары предполагает, подачу разных видов нефтей из
отдельных резервуаров, где они анализируются, а затем насосами подаются в
нужных количествах в узел смешения. Приготовленная в нем смесь забирается
специальными насосами и прокачивается по схеме резервуар - насос –
резервуар до тех пор, пока не будет получена однородная смесь,
соответствующая требуемому качеству. При необходимости в нее добавляется
тот или иной компонент, для достижения необходимых показателей. Наиболее
эффективным является приготовление продукции смешением в потоке.
Различные нефти и выделенные из них соответствующие фракции
отличаются друг от друга физико-химическими и товарными свойствами. Так,
бензиновые фракции некоторых нефтей характеризуются высокой
концентрацией ароматических, нафтеновых или изопарафиновых
углеводородов и поэтому имеют высокие октановые числа, тогда как
бензиновые фракции других нефтей содержат в значительных количествах
парафиновые углеводороды и имеют очень низкие октановые числа. Важное
значение в дальнейшей технологической переработке нефти имеет серность,
масляничность смолистость нефти и др. Таким образом, существует
необходимость отслеживания качественных характеристик нефтей в процессе
транспортировки, сбора и хранения с целью недопущения потери ценных
свойств компонентов нефти.
Однако раздельные сбор, хранение и перекачка нефтей в пределах
месторождения с большим числом нефтяных пластов весомо осложняет
нефтепромысловое хозяйство и требует больших капиталовложений. Поэтому
близкие по физико-химическим и товарным свойствам нефти на промыслах
смешивают для получения необходимой концентрации и направляют на
совместную переработку.
Таким образом,
для пропорционального смешивания двух разных
сортов нефтей, с целью получения нефти на заданную плотность, в проекте
расширения нефтеналивного терминала пред усматривается установка уз ла
с м е ш е н и я ( с м р и с ун о к 1.2) . С м е ш е н и е н е ф т е й п р о и с х о д и т п р и п о м о щ и
д в ух д о з и р ую щ и х насосов, подающих нефть в общий коллектор диаметром
400мм. Требуемое регулирование - в диапазоне дозирования от 30 до 200 М3/час.
Необходимо отметить, что смешение нефтей экономически целесообразно, так
как технологическое оборудование нефтеперерабатывающего завода
рассчитано на нефть определенной плотности (определенного сорта) и при не
соблюдении этого важного параметра будет нарушена вся сложная
технологическая цепочка получения конечного продукта, что приведет к
низкой эффективности переработки сырья либо получению
низкокачественного нефтепродукта [1].
Рисунок 1.2 – Схема технологических операций получения товарной
нефти
1.5 Подходы разработке АСУ узла смешения нефти и структура
управления
Целями создания АСУ узла смешения нефти являются [2]:
- модернизация уже существующей и создание новой АСУ
технологического процесса;
- повышение оперативности контроля технологического процесса;
- обеспечение бесперебойности технологического процесса;
- локализация аварийных участков и аварий оборудования;
- повышение эксплуатационных характеристик и надежности функцио-
нирования технологического оборудования;
- повышение безопасности функционирования технологического про-
цесса;
- повышение уровня автоматизации операций контроля и защиты за счет
применения для сбора информации современных микропроцессорных
контроллеров и программного обеспечения;
- снижение потерь химических и нефтехимических продуктов за счёт их
учета на этапах приема, хранения и отгрузки;
- получения обобщенных параметров работы объекта;
- повышения эффективности работы обслуживающего персонала.
Система автоматизации предназначена обеспечивать выполнение задан-
ных функций в автоматическом режиме управления, под наблюдением
Рисунок 1.3 - Структура управления
Первый (нижний) уровень системы включает датчики, вторичные
показывающие приборы, блоки и органы управления, устанавливаемые по
месту. К нижнему уровню также относятся пульты местной и дистанционной
сигнализации и управления, которые устанавливаются на территории
комплекса.
Второй уровень состоит из 3-х подсистем:
- подсистема газообнаружения;
- подсистема управления оборудованием комплекса;
- подсистема автоматического пожаротушения;
Для связи с технологическими объектами управления в каждой
подсистеме предусмотрены ПЛК Delta V производства компании Emerson.
ПЛК монтируются в шкафах автоматики в помещении операторной.
ПЛК обеспечивают:
- сбор информации от датчиков, устанавливаемых по месту, и вторич-
ных приборов;
- обработку и передачу информации о состоянии объектов на верхний
уровень системы;
- автоматическое управление технологическим оборудованием и контро-
ль его работы;
- прием информации с верхнего уровня управления и формирование
управляющих воздействий на электроприводы исполнительных механизмов.
Третий уровень включает в себя рабочие места операторов на базе
персональных компьютеров со SCADA-системой, сервер хранения данных.
Электроснабжение компьютерной станции оператора, шкафа
автоматики и полевых приборов выполнено через ИБП, который обеспечивает
надежное питание без потери информации.
Компьютер, сервер и панель оператора имеют связь с контроллерами, по
сети Ethernet.
1.6 Сравнительных анализ различных систем автоматизации
Быстроменяющаяся экономическая ситуация и большое разнообразие
задач, встающих перед предприятиями в современных рыночных условиях,
изменили старые взгляды на СА производства. Сегодня от такой системы
требуется уже не только следить за ситуацией и управлять ТП. Крайне
необходимо иметь доступ к постоянному источнику информации целым
группам людей и получать информацию в удобной форме, чтобы принимать
конструктивные решения в вопросах управления производством в целом.
Современный рынок средств автоматизации предлагает широкий спектр
аппаратных и программных устройств для построения надежных и удобных в
эксплуатации систем. Одними из главных преимуществ АСУТП являются
снижение, вплоть до полного исключения, влияния так называемого
человеческого фактора на управляемый процесс, сокращение персонала,
минимизация расходов сырья, улучшение качества исходного продукта, и в
конечном итоге существенное повышение эффективности производства.
Основные функции, выполняемые подобными системами, включают в себя
контроль и управление, обмен данными, обработку, накопление и хранение
информации, формирование сигналов тревог, построение графиков и отчетов.
Проведем анализ основных особенностей промышленных контроллеров,
которые согласно зарубежной терминологии делятся на три категории:
программируемые логические контроллеры (ПЛК), распределенные
управляющие системы (distributed control systems DCS) и контроллеры на базе
РС- технологий (PC-based).
ПЛК представляют собой устройство, предназначенное для сбора,
преобразования, обработки, хранения информации и выработки команд
управления. Они реализованы на базе микропроцессорной техники и работают
в локальных и распределенных системах управления в РВ в соответствии с
заданной программой. От небольших до мощных и высокоскоростных систем
ПЛК обеспечивают самых требовательных заказчиков исчерпывающими
возможностями и гибкостью при реализации современных сетевых решений в
распределенных системах управления и контроля. По техническим
возможностям, которые определяют уровень решаемых задач, ПЛК делятся на
классы: нано, микро, малые, средние и большие. Первоначально они
предназначались для замены релейно-контактных схем, собранных на
дискретных компонентах – реле, счетчиках, таймерах, элементах жесткой
логики.
Программировать ПЛК, как правило, можно на пяти языках стандарта
IEC-61131.3. Для тех, кто привык к релейно-контактным схемам, будет удобно
работать с языком, созданном на их основе (Ladder Diagram), тем, кому
понятней электронные схемы, могут воспользоваться языком
функциональных блоковых диаграмм (Functional Block Diagram). Опытные
программисты могут использовать возможности всех языков. Современный
ПЛК может обрабатывать дискретные и аналоговые сигналы, управлять
клапанами, шаговыми двигателями, сервоприводами, преобразователями
частоты, осуществлять регулирование (ПИД регулятор). Высокие
эксплуатационные характеристики делают целесообразным применение ПЛК
везде, где требуется логическая обработка сигналов от датчиков. Применение
ПЛК обеспечивает высокую надежность, простое тиражирование
обслуживание устройств управления, ускоряет монтаж и наладку
оборудования, обеспечивает быстрое обновление алгоритмов управления (в
том числе и на работающем оборудовании) [3].
При всем многообразии выбора технических средств в настоящее время
сформировались два основных класса промышленных контроллеров в
соответствии с выбором программно-аппаратной платформы низового уровня
автоматизации:
- пользователи, считающие, что задачи АСУТП должны базироваться на
классических системах РВ, основой которых служат ОСРВ, такие как OS-9,
VxWorks, LynxOS (UNIX РВ), QNX и др., и микроконтроллерах и микро-
процессорах таких производителей как Motorola (семейство МС 68***,
PowerPC), Siemens и др;
- пользователи, ориентированные на технологии PC/AT (PC-based), от-
дающие при решении любых задач, в том числе АСУТП, предпочтение связке
Intel - Microsoft.....
Введение
1 Описание технологического объекта, и сравнительный анализ систем
его автоматизации
1.1 Назначения и производственная программа терминала
1.2 Функциональное описание терминала
1.3 Технологическое, функциональное описание узла (участка)
смешения нефти
1.4 Подходы разработки АСУ узла смешения нефти и структура
управления
1.5 Сравнительных анализ различных систем автоматизации
1.6 Цель дипломного проекта
2 Рассмотрение структуры производственного процесса и разработка
функциональной схемы автоматизации узла смешения нефти
2.1 Макроанализ
2.2 Микроанализ
2.3 Построение функциональной схемы автоматизации. Спецификация
электрических, электронных и электронно-механических устройств
автоматической системы управления
2.4 Синтез комплекса технических средств
3 Визуализация экрана АРМ оператора в SCADA системе Trace Modе
3.1 Выбор режима управления
3.2 Задание технологических параметров
3.3 Задание параметров работы оборудования
3.4 Условия пуска оборудования
3.5 Пуск оборудования
3.6 Процесс работы оборудования
3.7 Автоматическая остановка работы оборудования (окончание
производства)
3.8 Аварийная остановка работы оборудования оператором
(аварийное прерывание производства)
3.9 Сообщение об аварии
3.10 Контроль работы оборудования
3.11 Ручной режим управления.
4 Безопасность жизнедеятельности
4.1 Анализ условий труда при эксплуатации узла смешения нефти
4.2 Расчет защитного зануления оборудования
4.3 Расчет эффективности акустической виброизоляции насоса смешения
нефти
5.Экономическая часть. Экономическая эффективность автоматизации
узла смешения нефти.
5.1 Технологическое описание процесса
5.2 Определение затрат в системах автоматизации
5.3 Определение затрат на оборудование
Заключение
Список принятых сокращений
Список литературы
Приложение А Функциональная схема автоматизации
1 Описание технологического объекта, и сравнительный анализ
систем его автоматизации
1.1 Назначения и производственная программа терминала
Нефть из месторождения железнодорожным транспортом поступает на
одностороннюю сливно – наливную эстакаду, сливается в резервуар хранения
нефти. Далее производится дополнительная подготовка нефти на установке
компаундирования (смешения), после чего нефть отправляется железно-
дорожным транспортом до конечных потребителей. Компаундирование
проводится с целью получения нефти на заданную плотность, определенного
сорта.
Производственная программа терминала предусматривает
строительство пускового комплекса нефтеналивного терминала с
грузооборотом 300 тыс. тонн в год на базе существующей нефтебазы.
Проектируемое предприятие (терминал) предусматривает выполнение
следующих операций:
- прием, хранение и отгрузку железнодорожным транспортом светлых
нефтепродуктов в объеме 110 тыс. тонн/год, в том числе бензина - 20 тыс.
тонн/год, дизельного топлива - 90 тыс.тонн/год;
- прием, хранение и отгрузку железнодорожным транспортом темных
нефтепродуктов в объеме 70 тыс. тонн/год, в том числе мазута М-100 в объеме
40 тыс. тонн/год, печного топлива – 30 тыс. тонн/год;
- прием, хранение и отгрузку железнодорожным транспортом нефти в
объеме 120 тыс. тонн в год;
- подготовку (смешение) нефти в объеме 120 тыс. тонн в год, с учетом
возможного увеличения до 200 тыс. тонн/год.
В данном дипломном проекте рассматривается именно смешение
нефти, как отдельный участок этого технологического процесса.
1.2 Функциональное описание терминала
Для обеспечения производственной программы и приведения
производства в соответствие нормам и правилам проектом предусматривается
следующая схема работы нефтеналивного терминала (см. рисунок 1.1).
а) Прием вагоноцистерн с бензином и дизельным топливом на
одностороннюю сливно-наливную ж/д эстакаду на 10 вагоноцистерн.
Предусмотрена возможность операции слива (налива) светлых
нефтепродуктов одновременно с двух вагоноцистерн.б) Прием вагоноцистерн
с мазутом или вязкой нефтью на туже одностороннюю сливно-наливную ж/д
эстакаду на 10 вагоноцистерны.
Рисунок 1.1 – Схема технологических операций терминала
Предусмотрена возможность операции слива (налива) разогретого
мазута или вязкой нефти с двух вагоноцистерн (цистерны оборудованы
паровой рубашкой).
в) Прием вагоноцистерн с легкой нефтью на туже одностороннюю
сливо-наливную ж/д эстакаду на 10 вагоноцистерн. Предусмотрена
возможность операции слива (налива) легкой нефти одновременно с шести
вагоноцистерн.
г) Прием вагонорцистерн с печным топливом на туже одностороннюю
сливо-наливную ж/д эстакаду на 10 вагоноцистерн. Предусмотрена
возможность операции слива (налива) печного топлива одновременно двух
вагоноцистерн, согласно графику приема-отпуска. Прием печного топлива
после отгрузки мазута предусматривает зачистку труб и оборудования. Прием
мазута и печного топлива происходит поочередно.
д) Хранение бензина в проектируемом резервуарном парке РВС – 5000
3
ж) Хранение дизельного топлива в проектируемом резервуарном парке
РВС- 5000 м3.
з) Хранение печного топлива в проектируемом резервуарном парке РВС
- 10000м3.
и) Хранение нефти в проектируемом резервуарном парке РВС - 10000
3
к) Перекачка нефти и нефтепродуктов с ж/д эстакад в резервуарные
парки при помощи насосов.
л) Отгрузка нефти и нефтепродуктов на ж/д эстакаду при помощи
насосов.
м) Внутрибазовые перекачки нефти и нефтепродуктов.
н) Товарная подготовка нефти в узле смешения.
п)Анализ нефтепродуктов в химической лаборатории.
1.4 Технологическое, функциональное описание узла (участка)
смешения нефти
Смешение в нефтеперерабатывающей промышленности используется на
разных стадиях переработки, для получения автомобильных бензинов
используют 10-15 компонентов.
Смешение осуществляется на специальных установках, используя
циркуляционный способ – приготовление производится в смесительных
резервуарах, смешение в аппаратах с перемешивающими устройствами либо
непосредственное смешение в трубопроводах.
Разработке узла приготовления товарной продукции должен
предшествовать расчет ожидаемых показателей качества товарных продуктов
на основе сведений о качестве отдельных компонентов.
Способ приготовления товарной продукции циркуляцией через
смесительные резервуары предполагает, подачу разных видов нефтей из
отдельных резервуаров, где они анализируются, а затем насосами подаются в
нужных количествах в узел смешения. Приготовленная в нем смесь забирается
специальными насосами и прокачивается по схеме резервуар - насос –
резервуар до тех пор, пока не будет получена однородная смесь,
соответствующая требуемому качеству. При необходимости в нее добавляется
тот или иной компонент, для достижения необходимых показателей. Наиболее
эффективным является приготовление продукции смешением в потоке.
Различные нефти и выделенные из них соответствующие фракции
отличаются друг от друга физико-химическими и товарными свойствами. Так,
бензиновые фракции некоторых нефтей характеризуются высокой
концентрацией ароматических, нафтеновых или изопарафиновых
углеводородов и поэтому имеют высокие октановые числа, тогда как
бензиновые фракции других нефтей содержат в значительных количествах
парафиновые углеводороды и имеют очень низкие октановые числа. Важное
значение в дальнейшей технологической переработке нефти имеет серность,
масляничность смолистость нефти и др. Таким образом, существует
необходимость отслеживания качественных характеристик нефтей в процессе
транспортировки, сбора и хранения с целью недопущения потери ценных
свойств компонентов нефти.
Однако раздельные сбор, хранение и перекачка нефтей в пределах
месторождения с большим числом нефтяных пластов весомо осложняет
нефтепромысловое хозяйство и требует больших капиталовложений. Поэтому
близкие по физико-химическим и товарным свойствам нефти на промыслах
смешивают для получения необходимой концентрации и направляют на
совместную переработку.
Таким образом,
для пропорционального смешивания двух разных
сортов нефтей, с целью получения нефти на заданную плотность, в проекте
расширения нефтеналивного терминала пред усматривается установка уз ла
с м е ш е н и я ( с м р и с ун о к 1.2) . С м е ш е н и е н е ф т е й п р о и с х о д и т п р и п о м о щ и
д в ух д о з и р ую щ и х насосов, подающих нефть в общий коллектор диаметром
400мм. Требуемое регулирование - в диапазоне дозирования от 30 до 200 М3/час.
Необходимо отметить, что смешение нефтей экономически целесообразно, так
как технологическое оборудование нефтеперерабатывающего завода
рассчитано на нефть определенной плотности (определенного сорта) и при не
соблюдении этого важного параметра будет нарушена вся сложная
технологическая цепочка получения конечного продукта, что приведет к
низкой эффективности переработки сырья либо получению
низкокачественного нефтепродукта [1].
Рисунок 1.2 – Схема технологических операций получения товарной
нефти
1.5 Подходы разработке АСУ узла смешения нефти и структура
управления
Целями создания АСУ узла смешения нефти являются [2]:
- модернизация уже существующей и создание новой АСУ
технологического процесса;
- повышение оперативности контроля технологического процесса;
- обеспечение бесперебойности технологического процесса;
- локализация аварийных участков и аварий оборудования;
- повышение эксплуатационных характеристик и надежности функцио-
нирования технологического оборудования;
- повышение безопасности функционирования технологического про-
цесса;
- повышение уровня автоматизации операций контроля и защиты за счет
применения для сбора информации современных микропроцессорных
контроллеров и программного обеспечения;
- снижение потерь химических и нефтехимических продуктов за счёт их
учета на этапах приема, хранения и отгрузки;
- получения обобщенных параметров работы объекта;
- повышения эффективности работы обслуживающего персонала.
Система автоматизации предназначена обеспечивать выполнение задан-
ных функций в автоматическом режиме управления, под наблюдением
Рисунок 1.3 - Структура управления
Первый (нижний) уровень системы включает датчики, вторичные
показывающие приборы, блоки и органы управления, устанавливаемые по
месту. К нижнему уровню также относятся пульты местной и дистанционной
сигнализации и управления, которые устанавливаются на территории
комплекса.
Второй уровень состоит из 3-х подсистем:
- подсистема газообнаружения;
- подсистема управления оборудованием комплекса;
- подсистема автоматического пожаротушения;
Для связи с технологическими объектами управления в каждой
подсистеме предусмотрены ПЛК Delta V производства компании Emerson.
ПЛК монтируются в шкафах автоматики в помещении операторной.
ПЛК обеспечивают:
- сбор информации от датчиков, устанавливаемых по месту, и вторич-
ных приборов;
- обработку и передачу информации о состоянии объектов на верхний
уровень системы;
- автоматическое управление технологическим оборудованием и контро-
ль его работы;
- прием информации с верхнего уровня управления и формирование
управляющих воздействий на электроприводы исполнительных механизмов.
Третий уровень включает в себя рабочие места операторов на базе
персональных компьютеров со SCADA-системой, сервер хранения данных.
Электроснабжение компьютерной станции оператора, шкафа
автоматики и полевых приборов выполнено через ИБП, который обеспечивает
надежное питание без потери информации.
Компьютер, сервер и панель оператора имеют связь с контроллерами, по
сети Ethernet.
1.6 Сравнительных анализ различных систем автоматизации
Быстроменяющаяся экономическая ситуация и большое разнообразие
задач, встающих перед предприятиями в современных рыночных условиях,
изменили старые взгляды на СА производства. Сегодня от такой системы
требуется уже не только следить за ситуацией и управлять ТП. Крайне
необходимо иметь доступ к постоянному источнику информации целым
группам людей и получать информацию в удобной форме, чтобы принимать
конструктивные решения в вопросах управления производством в целом.
Современный рынок средств автоматизации предлагает широкий спектр
аппаратных и программных устройств для построения надежных и удобных в
эксплуатации систем. Одними из главных преимуществ АСУТП являются
снижение, вплоть до полного исключения, влияния так называемого
человеческого фактора на управляемый процесс, сокращение персонала,
минимизация расходов сырья, улучшение качества исходного продукта, и в
конечном итоге существенное повышение эффективности производства.
Основные функции, выполняемые подобными системами, включают в себя
контроль и управление, обмен данными, обработку, накопление и хранение
информации, формирование сигналов тревог, построение графиков и отчетов.
Проведем анализ основных особенностей промышленных контроллеров,
которые согласно зарубежной терминологии делятся на три категории:
программируемые логические контроллеры (ПЛК), распределенные
управляющие системы (distributed control systems DCS) и контроллеры на базе
РС- технологий (PC-based).
ПЛК представляют собой устройство, предназначенное для сбора,
преобразования, обработки, хранения информации и выработки команд
управления. Они реализованы на базе микропроцессорной техники и работают
в локальных и распределенных системах управления в РВ в соответствии с
заданной программой. От небольших до мощных и высокоскоростных систем
ПЛК обеспечивают самых требовательных заказчиков исчерпывающими
возможностями и гибкостью при реализации современных сетевых решений в
распределенных системах управления и контроля. По техническим
возможностям, которые определяют уровень решаемых задач, ПЛК делятся на
классы: нано, микро, малые, средние и большие. Первоначально они
предназначались для замены релейно-контактных схем, собранных на
дискретных компонентах – реле, счетчиках, таймерах, элементах жесткой
логики.
Программировать ПЛК, как правило, можно на пяти языках стандарта
IEC-61131.3. Для тех, кто привык к релейно-контактным схемам, будет удобно
работать с языком, созданном на их основе (Ladder Diagram), тем, кому
понятней электронные схемы, могут воспользоваться языком
функциональных блоковых диаграмм (Functional Block Diagram). Опытные
программисты могут использовать возможности всех языков. Современный
ПЛК может обрабатывать дискретные и аналоговые сигналы, управлять
клапанами, шаговыми двигателями, сервоприводами, преобразователями
частоты, осуществлять регулирование (ПИД регулятор). Высокие
эксплуатационные характеристики делают целесообразным применение ПЛК
везде, где требуется логическая обработка сигналов от датчиков. Применение
ПЛК обеспечивает высокую надежность, простое тиражирование
обслуживание устройств управления, ускоряет монтаж и наладку
оборудования, обеспечивает быстрое обновление алгоритмов управления (в
том числе и на работающем оборудовании) [3].
При всем многообразии выбора технических средств в настоящее время
сформировались два основных класса промышленных контроллеров в
соответствии с выбором программно-аппаратной платформы низового уровня
автоматизации:
- пользователи, считающие, что задачи АСУТП должны базироваться на
классических системах РВ, основой которых служат ОСРВ, такие как OS-9,
VxWorks, LynxOS (UNIX РВ), QNX и др., и микроконтроллерах и микро-
процессорах таких производителей как Motorola (семейство МС 68***,
PowerPC), Siemens и др;
- пользователи, ориентированные на технологии PC/AT (PC-based), от-
дающие при решении любых задач, в том числе АСУТП, предпочтение связке
Intel - Microsoft.....
Толық нұсқасын 30 секундтан кейін жүктей аласыз!!!
Әлеуметтік желілерде бөлісіңіз:
Facebook | VK | WhatsApp | Telegram | Twitter
Қарап көріңіз 👇
Пайдалы сілтемелер:
» Туған күнге 99 тілектер жинағы: өз сөзімен, қысқаша, қарапайым туған күнге тілек
» Абай Құнанбаев барлық өлеңдер жинағын жүктеу, оқу
» Дастархан батасы: дастарханға бата беру, ас қайыру
Соңғы жаңалықтар:
» 2025 жылы Ораза және Рамазан айы қай күні басталады?
» Утиль алым мөлшерлемесі өзгермейтін болды
» Жоғары оқу орындарына құжат қабылдау қашан басталады?